【三工光学】「最高の掛け心地」を追求 鯖江市Part.2
鯖江漫遊記のPart.2、スタートです!
愛媛から車で約7時間以上、鯖江の看板を見ると私の心はマックスになっていました(笑)
私は緊張と興奮で、アドレナリンが・・・というお話は、ぜひこちらにて。
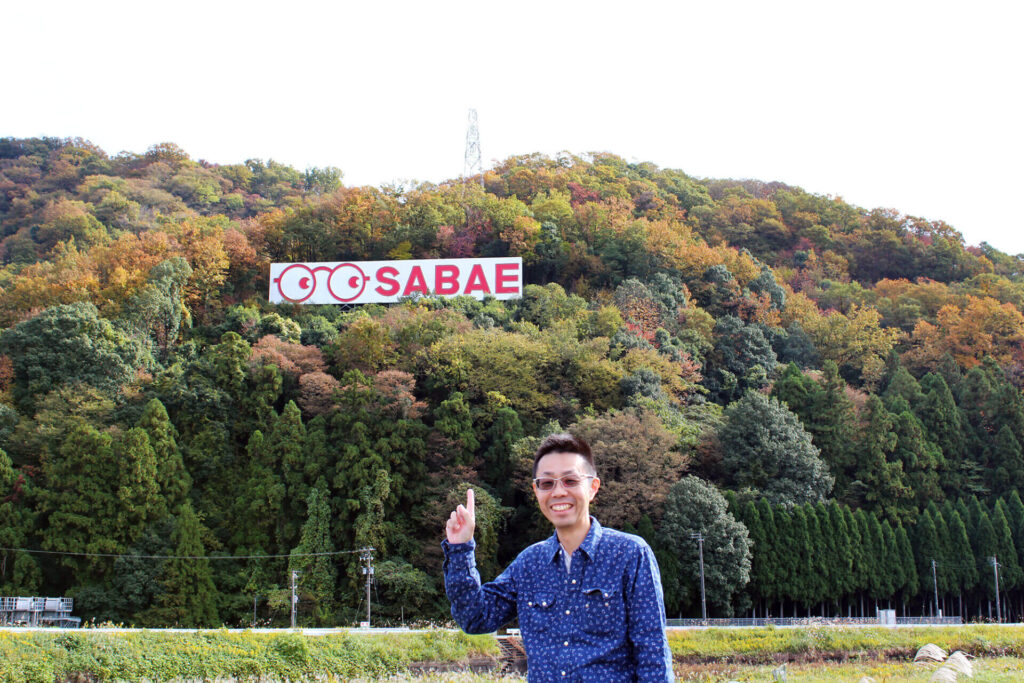
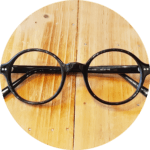
メガネで見えるようになりたい!
きっかけはいろいろだけど、見えにくいよりは見えたほうがいいですよね。
店舗でもメガネを作られて掛けられたとき、
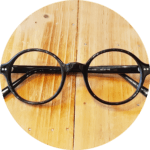
メガネで見あっ、よく見える!
って思わず出てしまう方が多いんですよ。
そして「よく見えるメガネ」が、「楽なメガネ」だったらうれしいですよね。
「よく見える」とは度数やフィッティングなどによりますが、だとしたら「楽なメガネ」とは?
それを教えてくれるのは、これからお伺いする三工光学様です。ぜひ最後まで読んでくださいね。
最高の掛け心地は手作業から生まれる「株式会社三工光学」
さて鯖江の空気を味わいつつ、長年お世話になっている株式会社三工光学様に向かいました。
1923年創業の三工光学様は、その歴史と共に築き上げられた素晴らしい技術をもたれており、メガネのアオノ松山店でも多くのフレームを扱わさせていただいています。
数年前までアオノまで来てくださった樋田さんとの再会で話に花が咲き、少し緊張が解けた私でした(笑)
樋田さんとの出逢いは十数年にもなり、私に眼鏡のイロハを教えてくださった方でもあります。
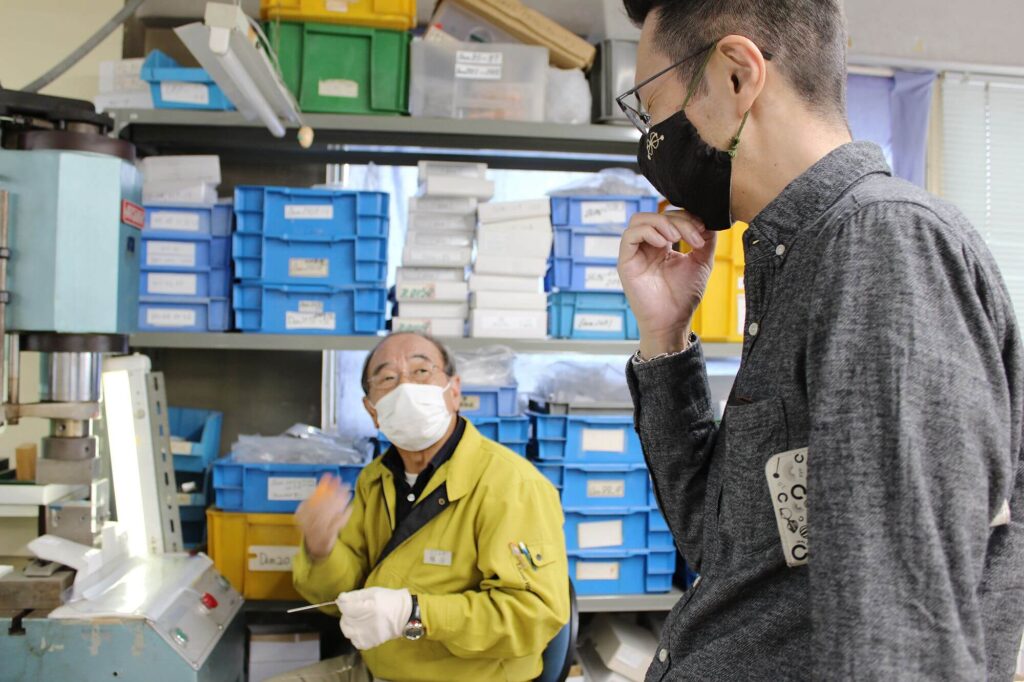
チタン素材をメガネに使うことに成功した鯖江の技術力
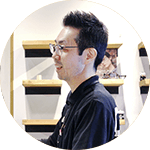
ここで質問です!!
-
フレームはどれくらいの工程を経て、またどのように作られているかわかりますか?
-
フレームが出来上がるまでには、およそ200~250の様々な工程を経て完成されます。また、ひとくちにフレームといっても、形状や素材によっても工程は違ってきます。
その工程の多さにびっくりです!そして私は、今の技術を用いた機械設備を入れつつも、そのほとんどが手作業だったことに驚きとともに感動しました。
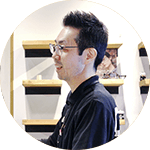
第2の質問!!
-
鯖江のフレームは、主に何の素材を使用しているでしょうか?
-
主にチタンになります。(※他の素材も使用しています)
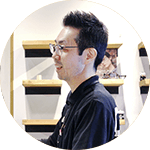
鉄の2倍も強度があるチタンが!?
そうなんです!
チタンは強度が高いだけではなく、しなりやすく少し曲げても元に戻る性質があります。そして錆びにくく、とにかく軽くて、体に優しい安全な金属です。
ちょっとした豆知識
チタンは大別すると純チタンとチタン合金の2種類で、その中にも多くの種類があります。眼鏡フレーム以外にも、自動車や自転車部品、医療器具や宇宙開発設備など世界中で幅広く活用されています。アレルギーが起こりにくく、有害性もないので、例えばインプラントや心臓弁など人体に使われています。眼鏡は顔にかけるものです。それだけ安心した素材を使用しているということがわかりますよね。
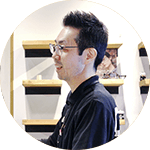
鉄チタン素材はめちゃくちゃすごい!
そうではあるのですが、高品質で幅広く使えるぶんコストがかかります。そのうえ、強度が高いので溶接やプレス成形、切削が難しく、難粗材とも言われています。だからこそ、チタンの特徴に合わせた加工方法と、高技術が必要になるというわけです。
従来加工が難しいとされていたチタン素材を、メガネに使うことに成功した鯖江の技術力はすごいものですね。
そしてチタンの中でも三工光学様が手掛けているのは、「GUMMETAL(ゴムメタル)」というトヨタグループのシンクタンクである豊田中央研究所が開発した新チタン合金です。
ゴムのようにしなやかで高強度、また腰も強く、一般のチタン合金よりも遥かに錆びにくく、しかも限りなく人体に優しいという特徴があります。
ゴムメタルは、ゴムなのか?メタル(金属)なのか?というと、ゴムのような非線形弾性変形を示す金属(チタン合金)です。
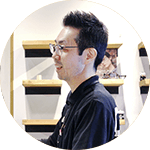
ゴムメタルが、どれくらいのしなやかさや弾力があるのか?
私たちがお客様に見ていただくのがこちらの道具です。ちなみに三工光学様からいただいたものです。
左から、チタン、Βチタン、ゴムメタルになります。ゴムメタルのしなやかさや弾力が、よく表れていると思います。
でも全てがゴムメタル使用ではなく、それぞれの特徴を生かしてフレームによって使い分けをしているんですよ。
さて、待ちにまった工場を見せていただくことに。
工場を案内してくださるのは、常務取締役 西川義孝(にしかわよしたか)様です。
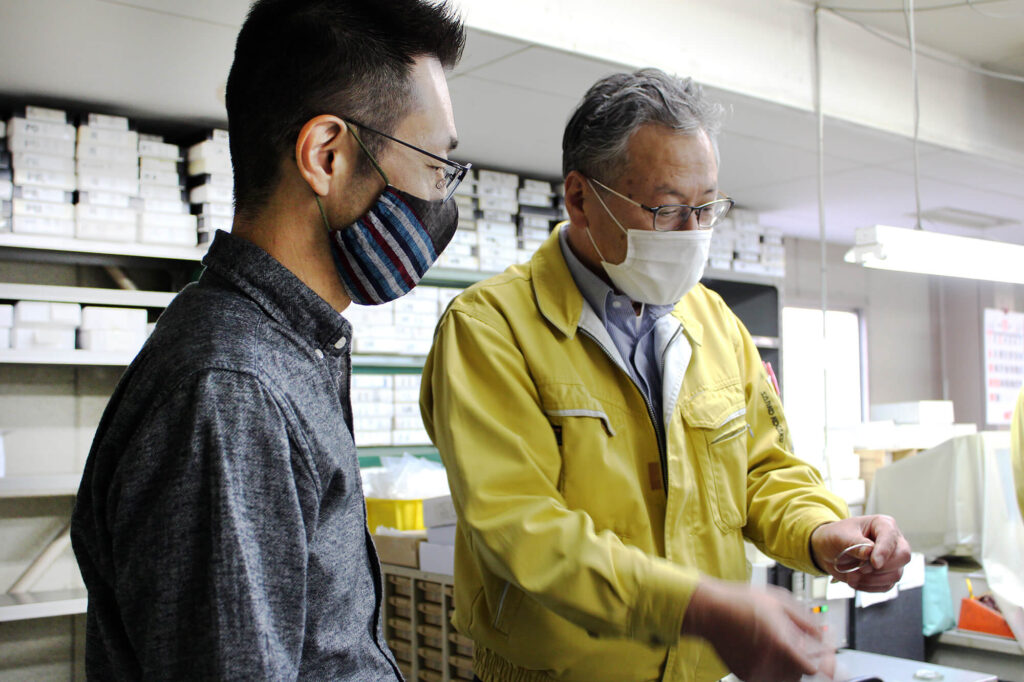
フレームの工程を見て知る
さて、話は工場に戻して。
フレームが作られる工程をざっくりとしか知らなかった私には、どれも目新しく感じました。これまで営業の方からの受け売りでお客様に伝えてきましたが、これからは「プラス」ができるような感じがします。
フレーム作成の工程をざっくりというと下記の流れになります。(※三工光学様内)
設計 → パーツ作成 → 溶接 → 磨く → 検品
- 1、設計
- デザインを商品化するために図面に落とし込んでいきます。
メガネを掛ける人の負担ができる限り少ないデザインの追求 + 素材を活かしたブランド
長年培ってこられた技術を活かすことができる三工光学様ならではの強みだと思います。
- 2、パーツ作成
- デザインを商品化するために図面に落とし込んでいきます。
メガネを掛ける人の負担ができる限り少ないデザインの追求 + 素材を活かしたブランド
長年培ってこられた技術を活かすことができる三工光学様ならではの強みだと思います。
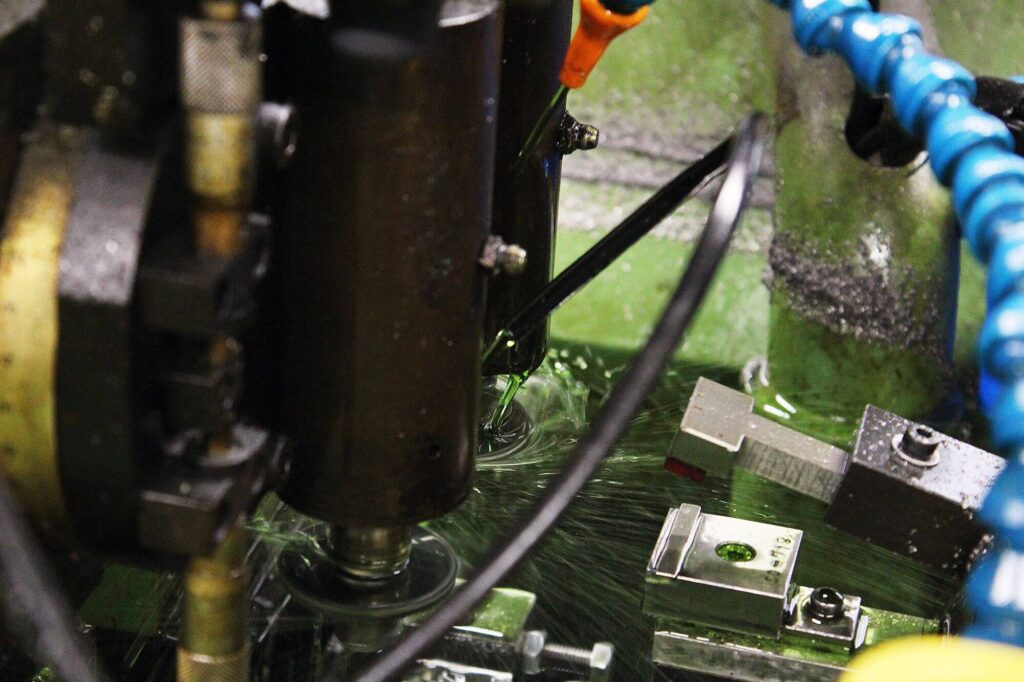
パーツ一つひとつを切削していきます
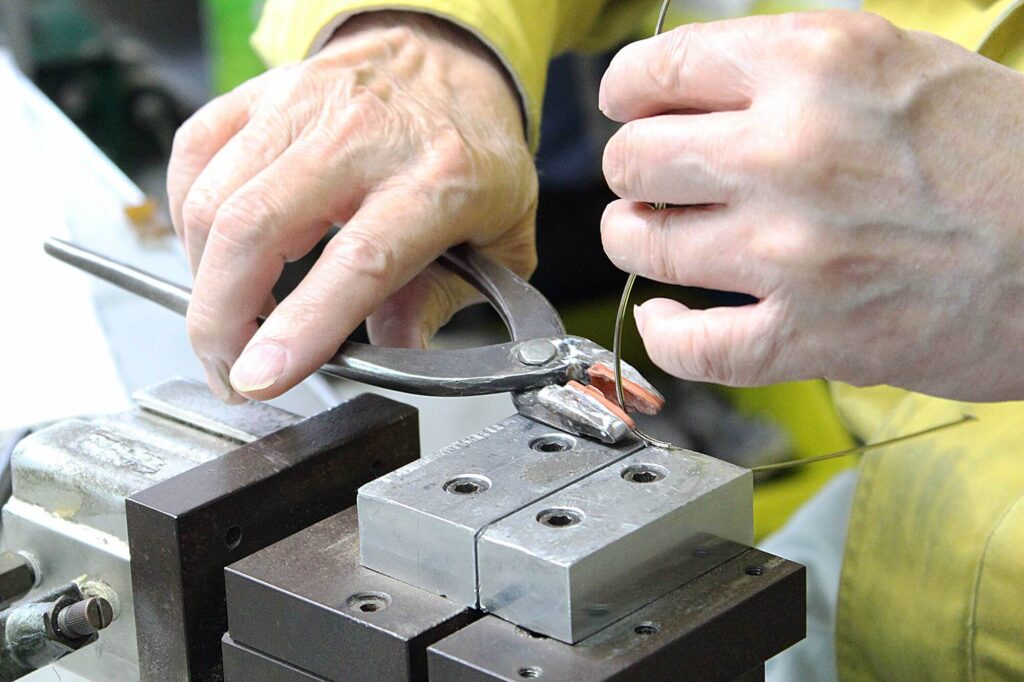
リム(レンズの周りを囲む枠の部分)の角度調整を行っています
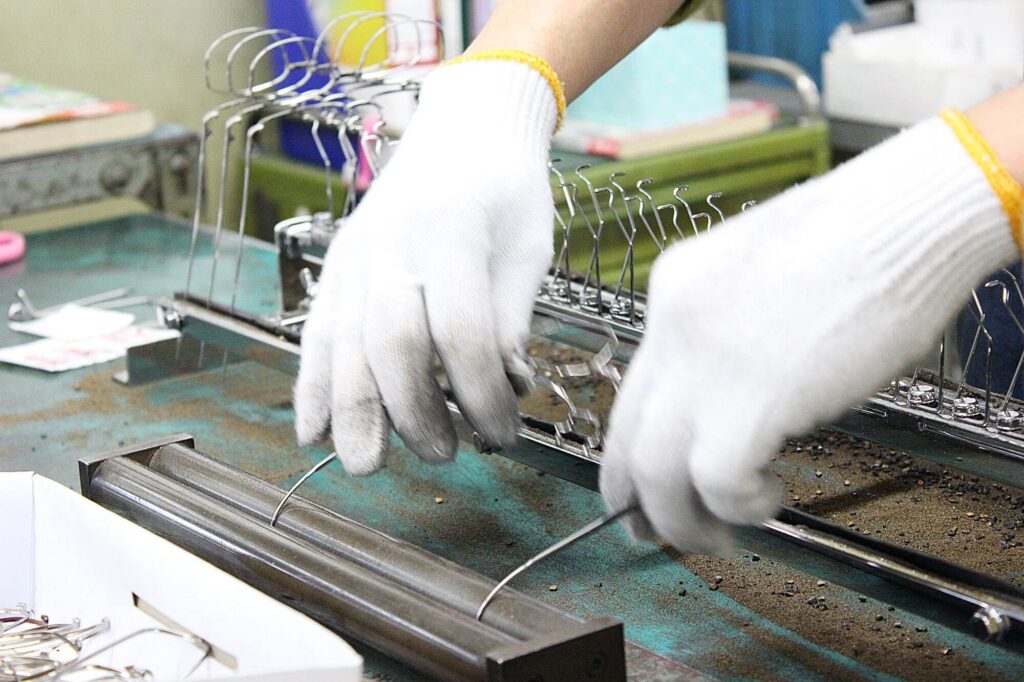
耳にかける部分の角度づけをしています
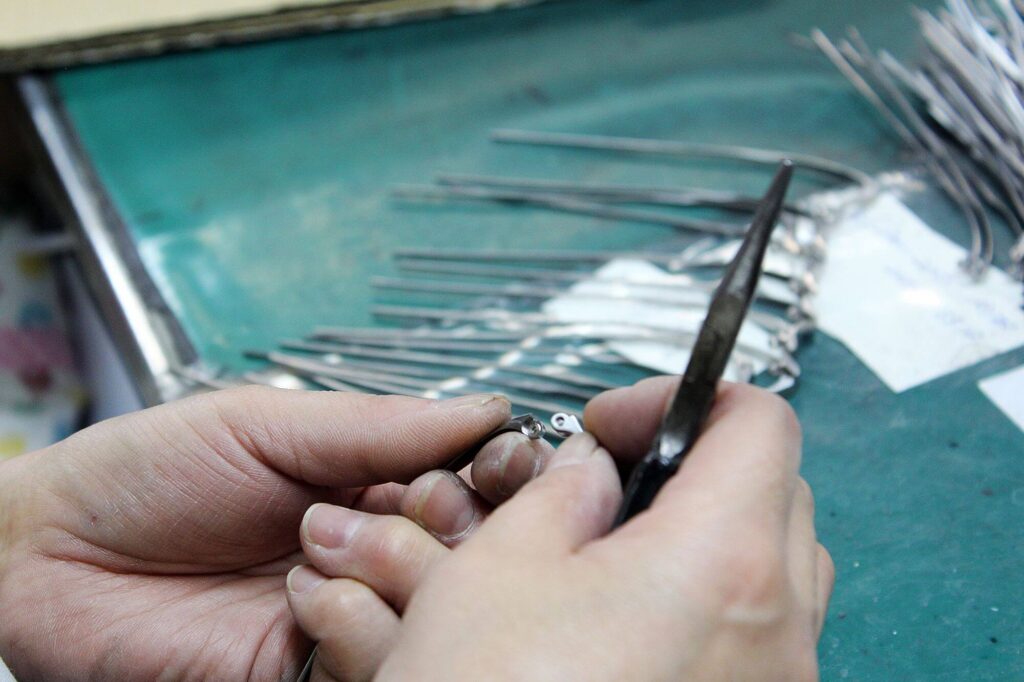
チタンテンプルの丁番(フロントとテンプルをつないで開閉する部分)部分にワッシャーを入れます
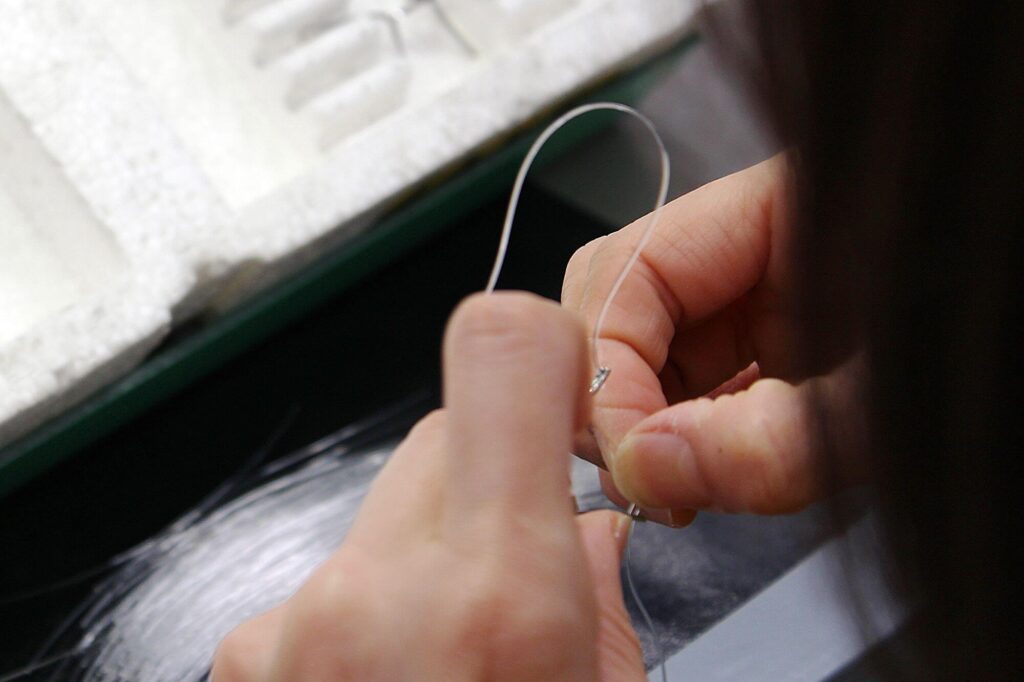
フロント(フレームの全面部)のナイロンを入れています
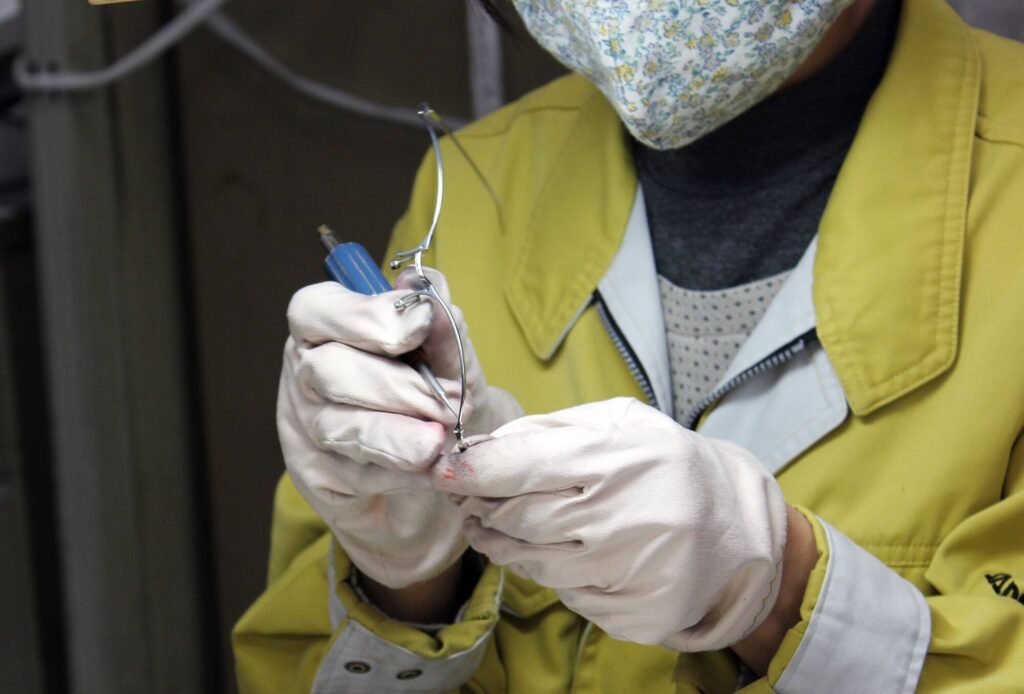
丁番に油を差しています
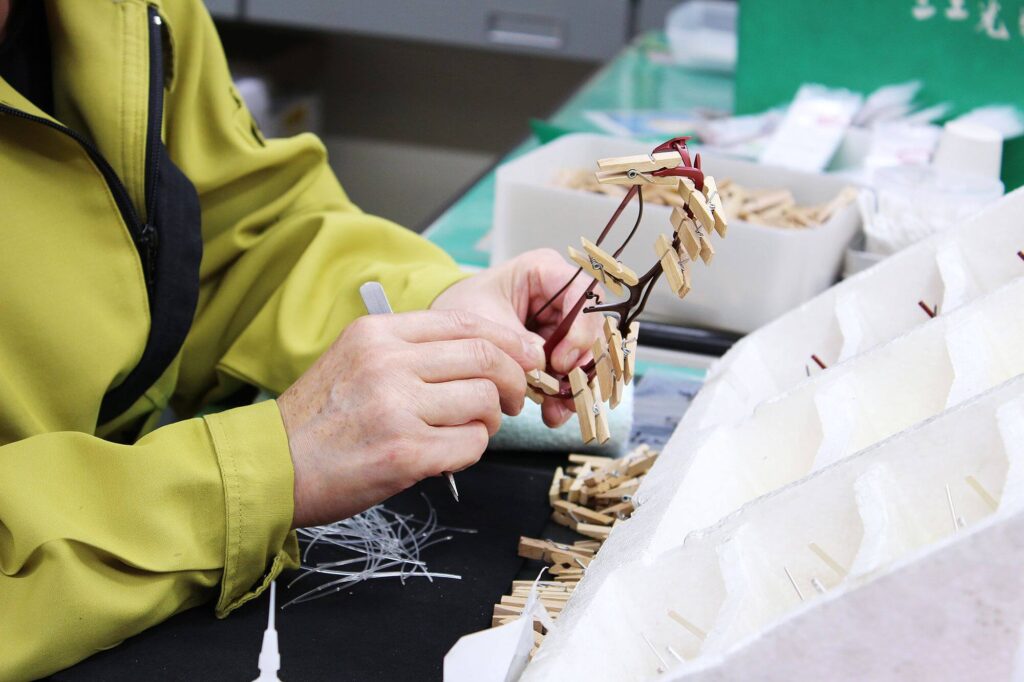
リムの内側にあるレールにナイロンを固定させています
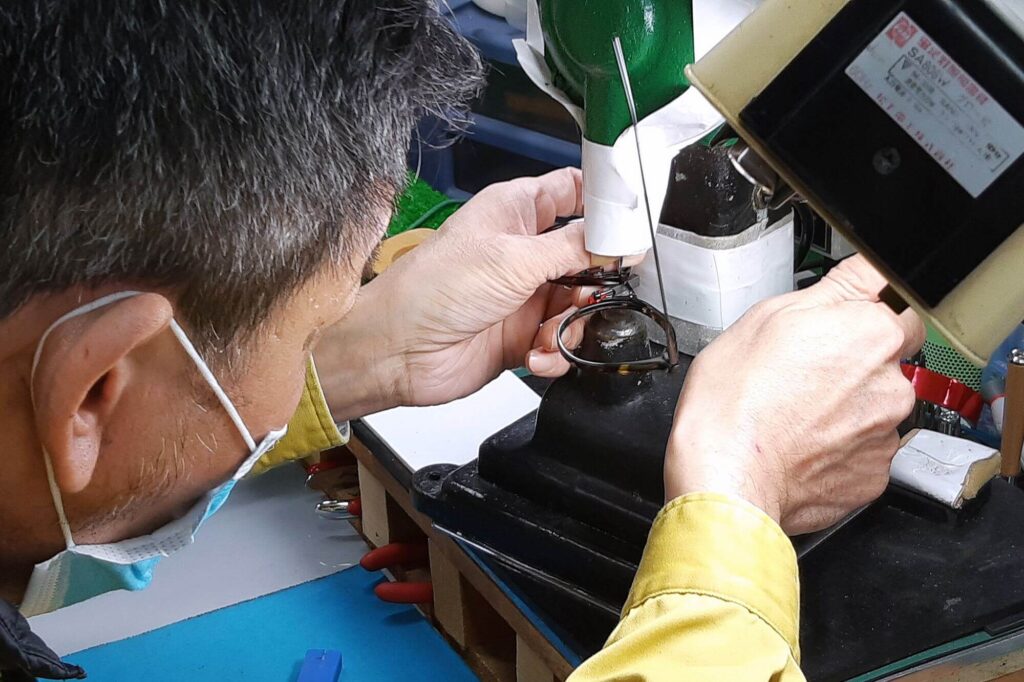
プラスチックフレームのピン取り付けを行っています
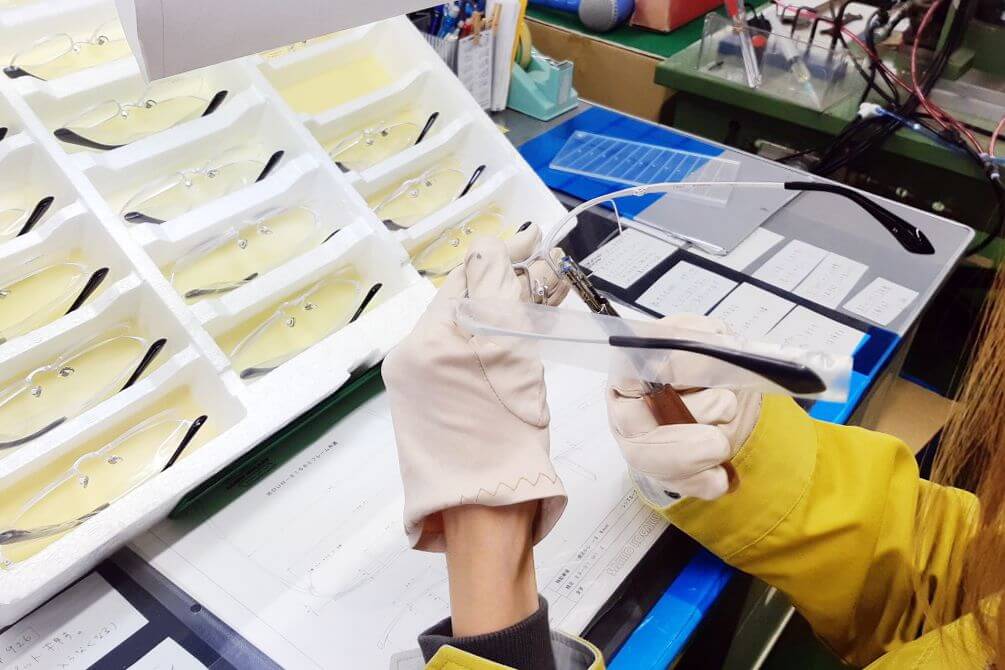
鼻パットの調整を行っています
こちらはフレームフロント部分のリム線(βチタン)を巻く機械です。レンズがきちんと収まるカーブを作り出すには、微妙な調整が必要となります。
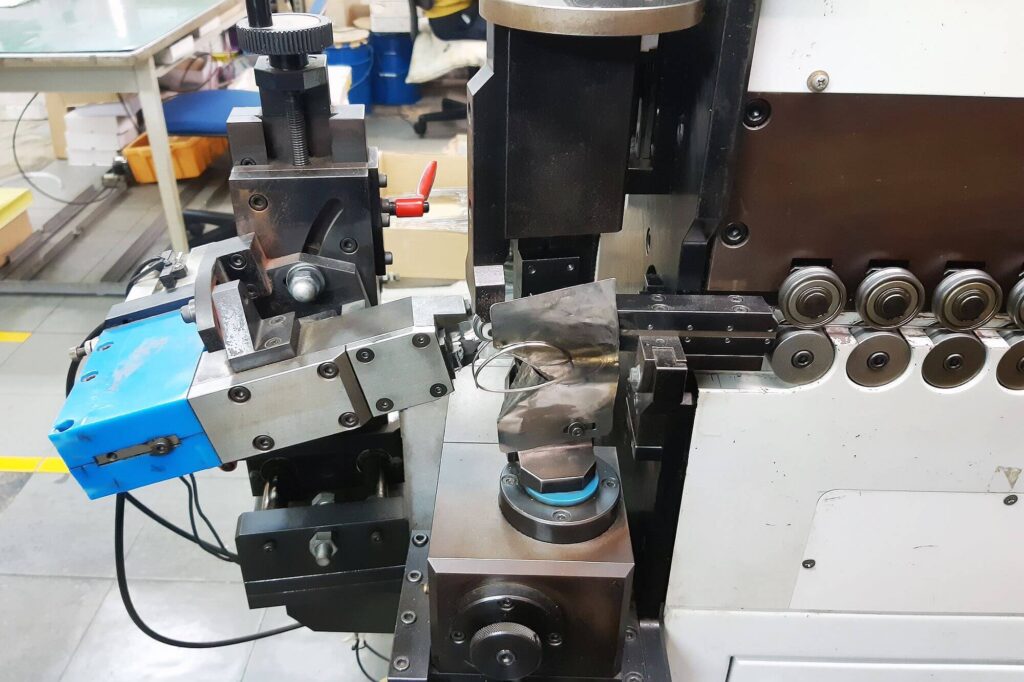
▼
- 3、溶接(ロー付け)
- 2つのパーツを接合しますが、その方法も様々です。とても細かい部品を扱うので、作業される方の細やかな感覚が要求されます。
こちらはクリングス(ノーズパッドとフレームをつなぐ部分)のロー付けです。空気が入らない状態にして、アルゴンガスを一気に噴射して溶接します。この治具(ちぐ)は自社開発であり、他にも多くの治具があるそうです。
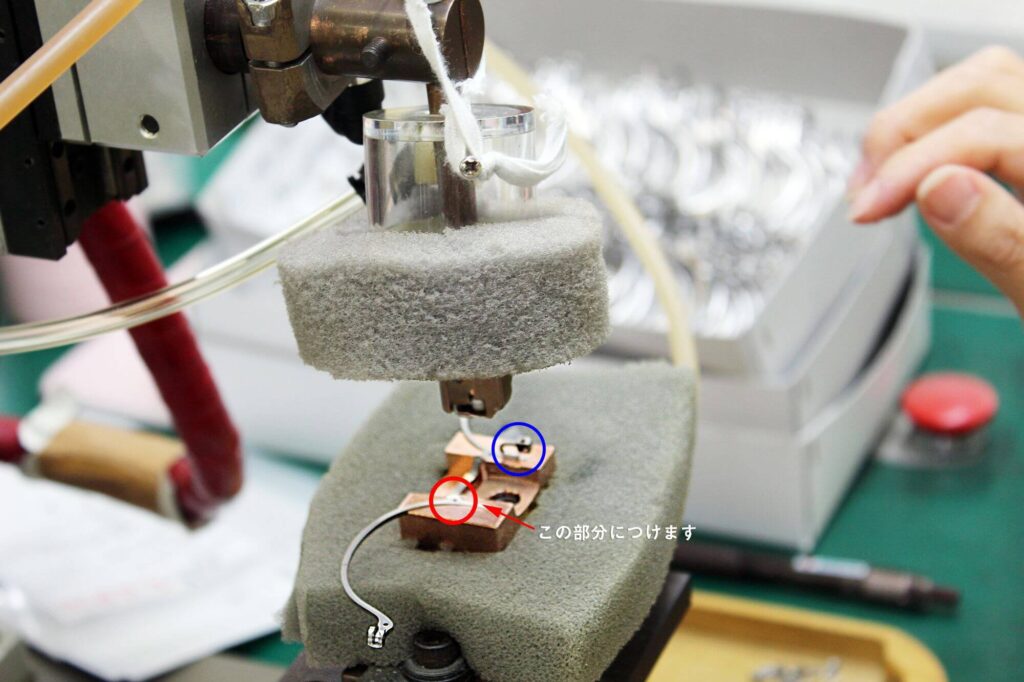
赤丸の部分に、クリングス(ノーズパッドとフレームをつなぐ部分)を取り付けます
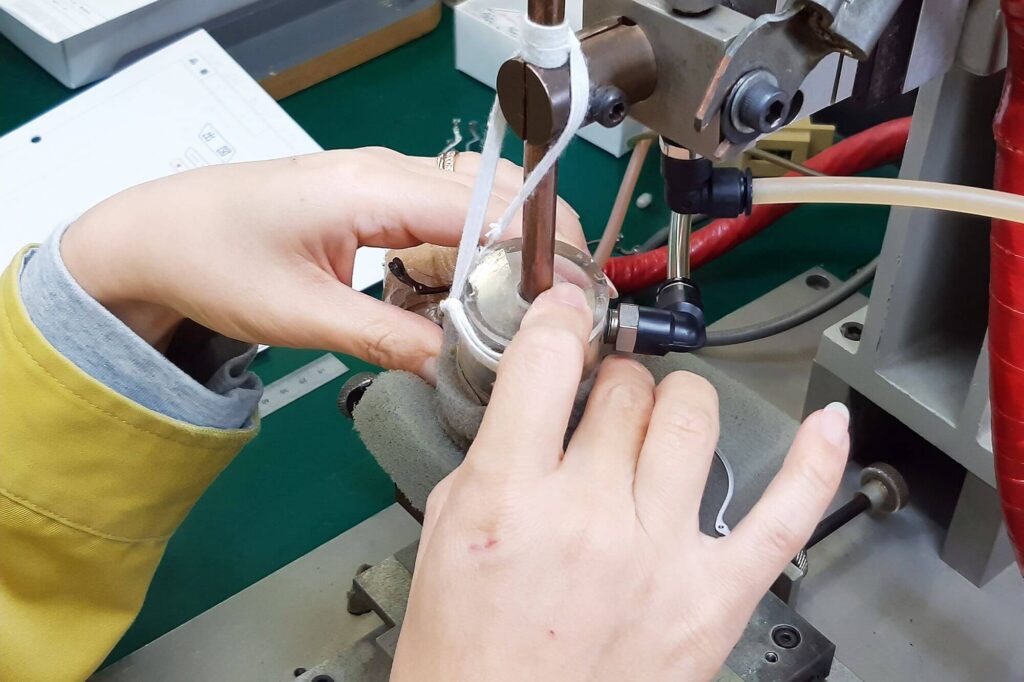
取り付けは一瞬です
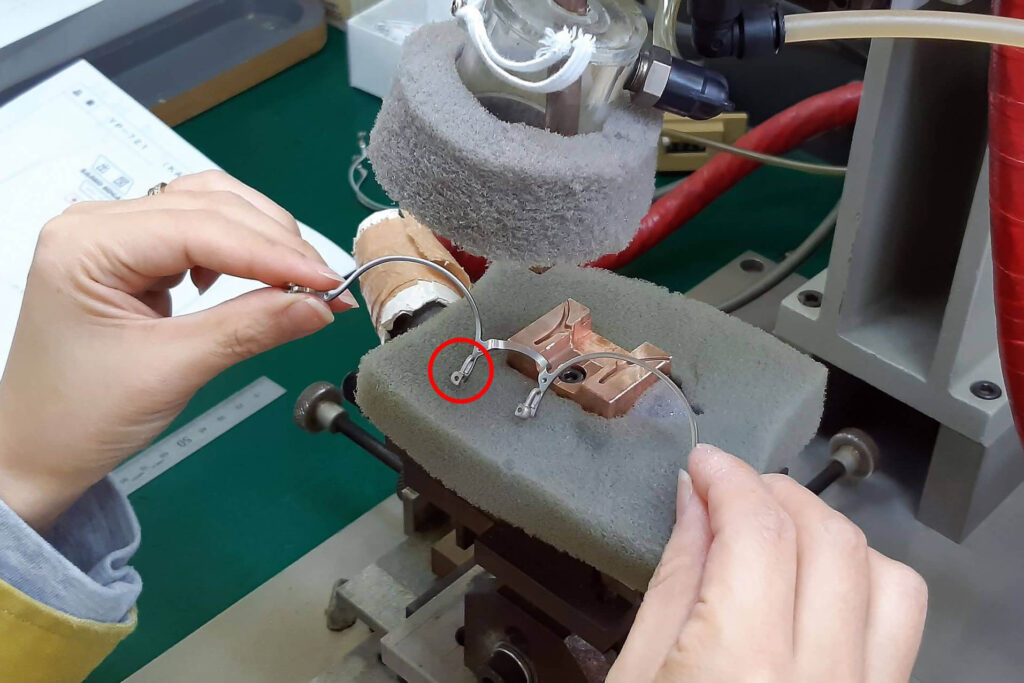
クリングスが取り付けられました
▼
- 4、磨く
- パーツを溶接した後は、フレームを専用ラックに掛け、研磨剤を入れた機械を回転させフレームを磨いていきます。段階を経て、きめ細かい研磨剤にて磨いていきます。
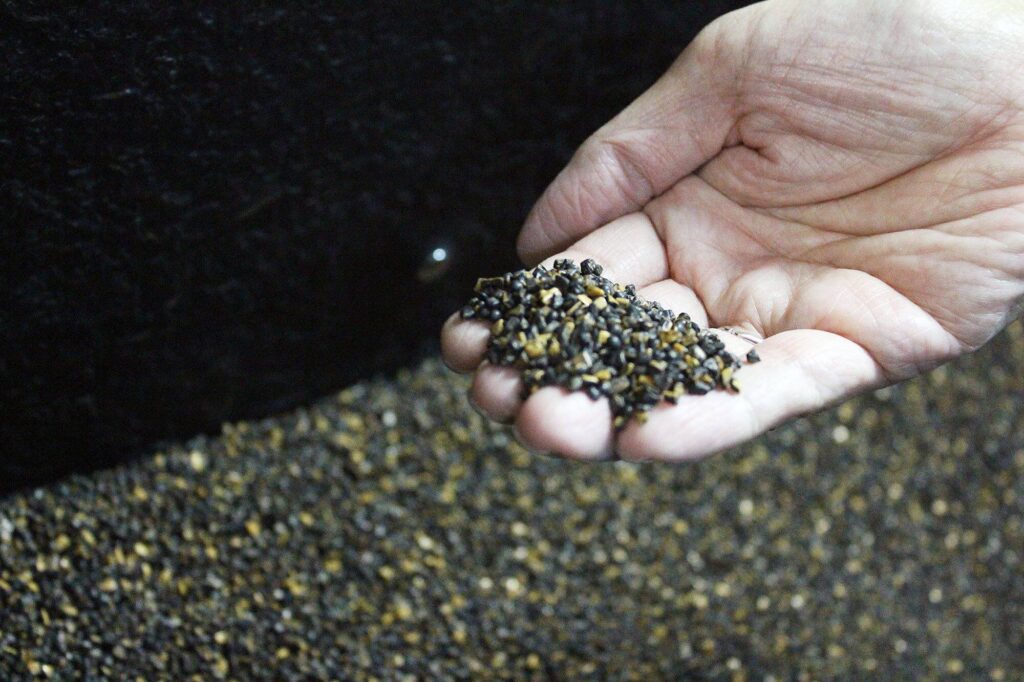
研磨剤の粒子は、段階を経て細かくなります
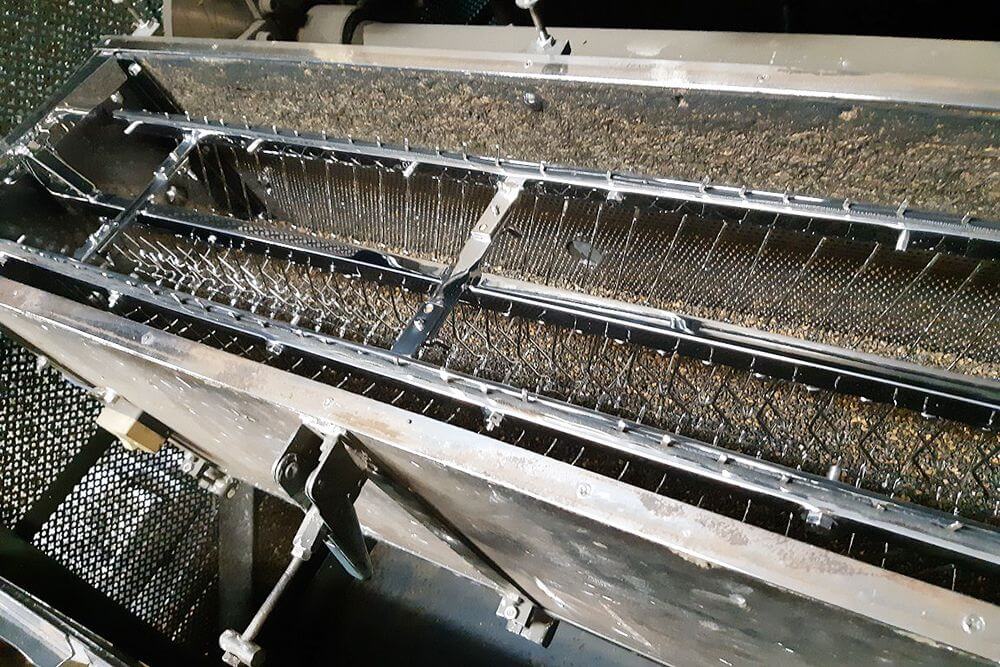
専用ラックにフレームをかけます
リングスが取り付けられました
手作業で磨きを行われていました。バフに当てる角度や時間など、熟練の技術を必要とされます。
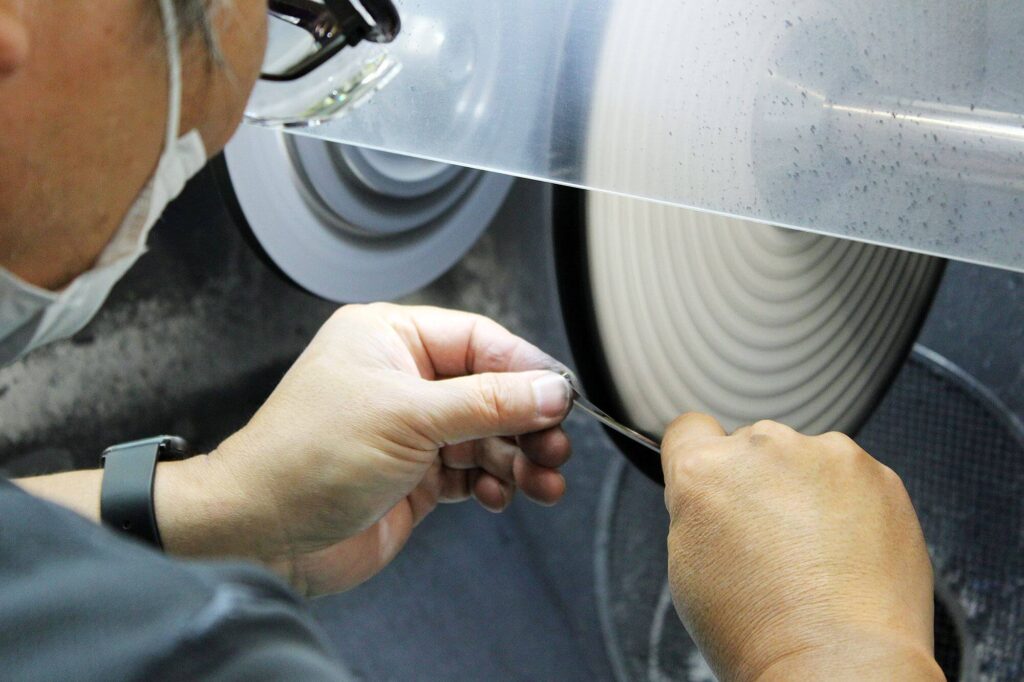
▼
- 5、検品
- 最終検品は、1枚(業界では眼鏡の数詞は「枚」と数えます)ずつ肉眼で厳しいチェックが行っていきます。キズなどがある場合はマーキングされ、再び工程を経て再チェックされます。
受け継がれ、新しいものを融合
そしてもう一つ、印象深く残っていることは、女性や若い方が多かったことです。一人ひとりが笑顔にあふれ、仕事に誇りを持っている姿は眩しく感じました。
長年築かれてきた職人の技術は若い人に受け継がれ、そこに新しいものを融合して今に至る、そしてまた未来へと。
私はそれを感じることができ、お伺いできたことを改めてよかったと思っています。
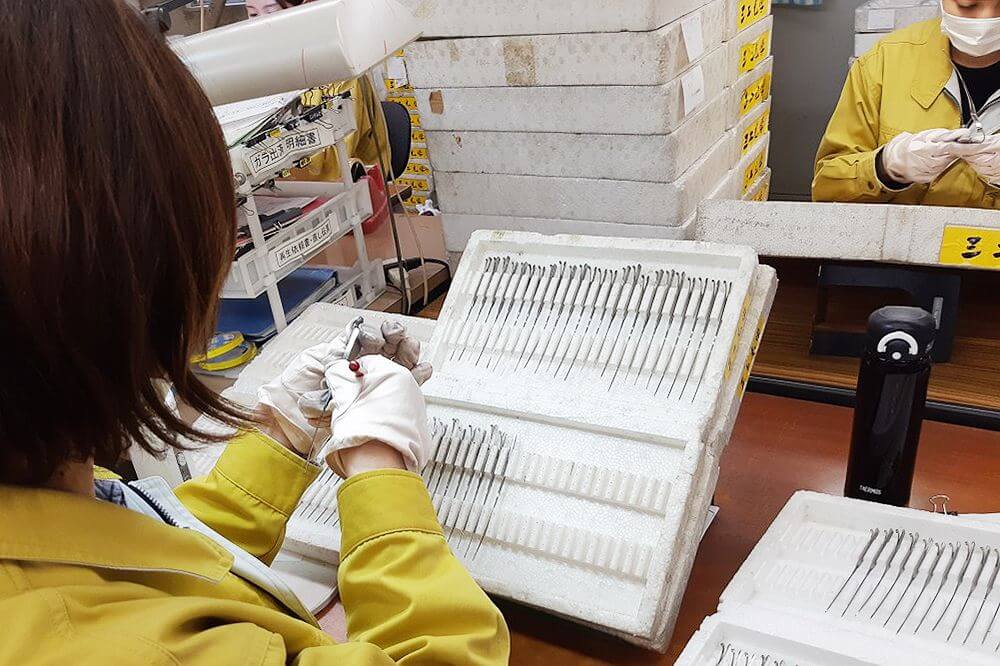
眼鏡を使うのはお客様
これまで24年、メガネを売ることが私の仕事でした。
これはこれからも変わることはない。でも、眼鏡を使うのはお客様です。そのお客様に何を伝えることができるのか、それを見直しさせてくれる貴重な経験ができたと思っています。
「楽なメガネ」というのは、「掛け心地のよさ」を追求されてこそ生まれるものです。それは素材はもちろんのこと、職人たちの目と手で丹念に作られているからこそ、眼鏡を使う人にとって「最高の掛け心地」となっているのです。
そして日常生活の相棒であるメガネは、使う頻度が高いからこそ、「曲がった!」などといったトラブルとも隣り合わせです。でも、驚くほど簡単に壊れることがない。それが、鯖江のフレームなのです。もちろん、年数や使用方法によって一概には言えませんが、鯖江(国産)ならではの素晴らしさではないでしょうか。
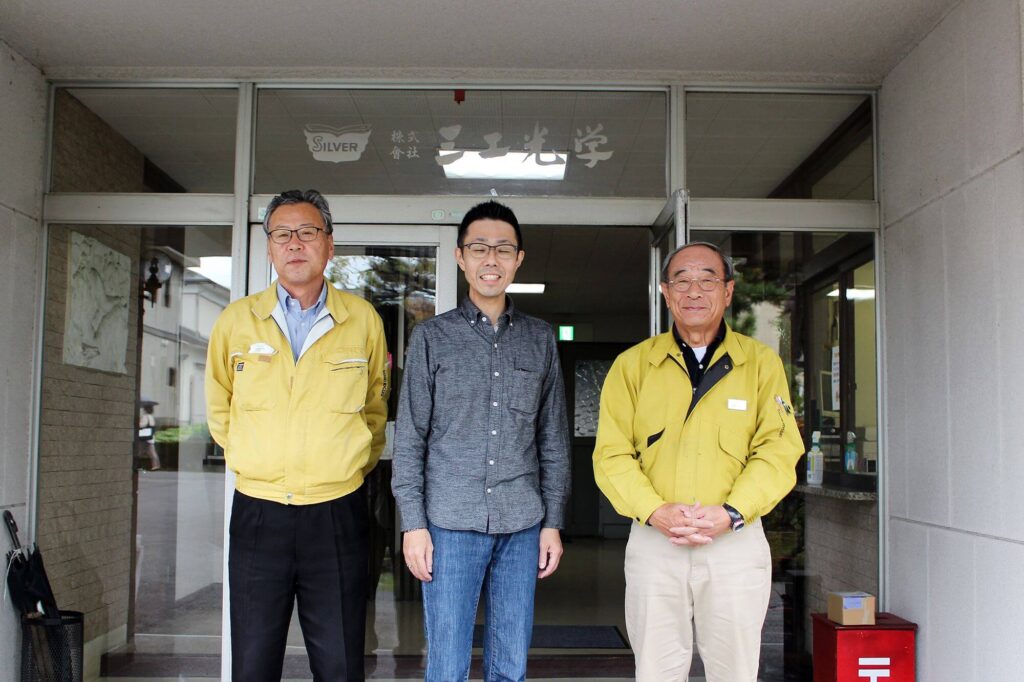
ゴムメタルを用いて掛け心地を追求したスタイリッシュフレーム「dun(ドゥアン)」
眼鏡業界にて24年。憧れの福井県鯖江市に向かう私の記事はこちら
眼鏡の聖地 福井県鯖江市に行ってきました!鯖江市Part.1
メガネの修理などをご依頼している株式会社リペア様の見学記事はこちら
【リペア】眼鏡の生産地である鯖江で修理 鯖江市Part.3
表面処理加工の高い技術を持つアイテック株式会社様の見学記事はこちら
【アイテック】表面処理加工で輝きをはなつ!高い技術力と想い 鯖江市Part.4